In the modern manufacturing landscape, success is no longer defined solely by output and profit margins. It’s about how well a facility integrates technology, safety, and people. One of the most strategic moves a plant manager or safety director can make is selecting a supplier that offers both machine safety solutions and industrial automation services. This integration not only streamlines operations and reduces risk—it also cultivates a more confident, engaged, and productive workforce.
1. The Evolving Definition of a "Better Factory" A "better factory" in 2025 means more than leaner processes and uptime—it reflects a workplace where safety, morale, and operational excellence align. Employees want to feel protected and valued. At the same time, leadership demands efficiency, data visibility, and scalable systems.
Choosing a single supplier that integrates both safety systems and automation solutions helps balance these needs. The result? A safer, smarter factory environment that enhances trust, transparency, and technological growth.
2. The Power of a Unified Solution: Machine Safety + Industrial Automation Most factories historically separated safety and automation into different departments or managed them with different vendors. This often resulted in:
Miscommunication between systems
Overlapping scopes of work
Safety upgrades that conflicted with automation goals
Delayed timelines and inflated budgets
But a single-source provider that integrates both solutions aligns the design, engineering, and implementation processes from the start.
Benefits of Unified Design: Coordinated system integration
Harmonized safety circuits with PLC and HMI programming
Real-time diagnostics that tie into SCADA and MES platforms
Better documentation for OSHA/ANSI audits
Fewer integration errors and startup issues
3. Reducing Human Error with Smart Safety Automation Factories often struggle with legacy machines or manually dependent systems that increase risk due to human error. By combining automation and safety, facilities can upgrade those pain points into smarter, safer processes.
Examples of Improvement: Light curtains or area scanners integrated with robotic cells that shut down processes without halting entire production lines.
Safety-rated PLCs and servo motors that enforce safe speeds and zones for collaborative operations.
Guarding systems that detect and communicate faults directly to HMIs or maintenance systems.
These technologies not only protect workers—they empower them to interact with machines confidently, reducing stress and uncertainty on the shop floor.
4. Empowering Workplace Culture Through Initiative-taking Safety When employees see investment in integrated machine safety and automation, it directly impacts their workplace attitudes. Why?
Because safety doesn’t feel like afterthought it’s embedded into operations.
Key Cultural Impacts: Improved morale: Workers feel valued when their well-being is clearly prioritized.
Higher retention: Technicians and operators are more likely to stay with companies that invest in both efficiency and protection.
Better engagement: Employees more actively participate in safety programs when technology supports their role.
According to a recent study by the National Safety Council, companies that invest in both automation and safety see up to a 25% increase in workforce engagement over five years.
5. Streamlining Training and Onboarding Training employees on both safety and machine functions can be time-consuming—especially when systems aren’t intuitive. But when the supplier unites automation systems and safety components, training becomes more efficient.
Unified Systems = Better Training: HMIs designed with built-in safety visuals
Step-by-step startup and shutdown sequences tied to interlocks and guarding
Role-specific access to controls and diagnostics (e.g., via RFID or badge scan)
This type of system design helps maintenance, production, and safety teams speak the same language, reducing onboarding time and the likelihood of errors.
6. Building Resilience with Scalable Solutions The integration of safety and automation is not just about day-one installation—it’s about long-term scalability. A vendor that offers both services ensures your systems grow with your needs.
Scalable Benefits: Easily add robots, conveyors, or new cells without redesigning safety systems
Centralized data logging for downtime, safety faults, and productivity metrics
Consistent control panel architecture across departments and facilities
Remote access and diagnostics across safety and automation layers
This scalability prepares factories for future expansions or tech migrations, like Industry 4.0 or AI-driven OEE tracking.
7. Case Example: Transforming a Legacy Plant with Integrated Safety + Automation Let us take the example of a packaging manufacturer that relied on older equipment and a manually operated line. After several near-miss incidents and rising downtime, they partnered with a supplier offering combined automation and safety solutions.
Before:
Outdated conveyor system with no interlocks
Operators fear due to exposed pinch points
Manual inspection with poor accuracy
Downtime averaging 18 hours/month.
After:
Interlocked custom guarding with access gates and safety-rated switches.
Visual indicator lights and E-stop stations
Camera-based inspection and servo control for packaging
Downtime reduced by 45%.
Employee satisfaction score increased 2.1 points (on a 5-point scale)
This integration led not only to fewer safety incidents but also to a noticeable shift in employee attitude and process ownership.
8. Compliance, Liability, and Risk Reduction Another major advantage of combining safety and automation systems is regulatory compliance. OSHA and ANSI standards expect facilities to show due diligence and systematic risk reduction efforts.
How Integration Helps: Documented safety logic programmed into automation platforms
Circuit validation with ISO 13849-1 and ANSI B11 standards
Safety relays and PLCs with diagnostics exported into plant-wide data logs.
Centralized reporting for compliance audits
When one vendor designs both the safety and automation architecture, it reduces gaps in coverage—and more importantly, it reduces liability for the company.
9. Faster Implementation and ROI Managing two separate vendors for safety and automation creates project bloat. When both solutions are provided under one roof, implementation timelines shrink, and ROI improves.
Financial and Timeline Benefits: Shorter project cycles (often by 30-50%)
Less time spent coordinating between teams.
Quicker ramp-up means faster production.
Lower overall system cost due to shared engineering hours.
Additionally, factories often unlock insurance benefits and grant eligibility when investing in holistic safety and automation upgrades—boosting ROI even further.
10. Choosing the Right Supplier: What to Look For Not all vendors are equipped to deliver integrated solutions. When evaluating a supplier, make sure they offer:
In-house engineering teams for both automation and safety Turnkey solutions—from risk assessments to installation ANSI/ISO/OSHA compliance expertise Robotic system integration capabilities Custom guarding, safety controls, and machine programming Documentation and training included in every project.
Power Safe Automation, for example, provides full-service integration that includes robotic automation, custom guarding, and compliant safety controls—all under one contract. This makes them an ideal single-source partner for factory-wide upgrades.
Final Thoughts: The Smartest Way to Build a Safer, Smarter Factory The choice to use a supplier that integrates machine safety and industrial automation isn’t just smart—it is transformative.
It simplifies your project management. It enhances your regulatory compliance. It empowers your workforce. It strengthens your long-term strategy.
In an industry that demands both productivity and accountability, this dual-focus approach is how manufacturers build facilities that are not only efficient—but also safe, scalable, and respected by the people who work in them.
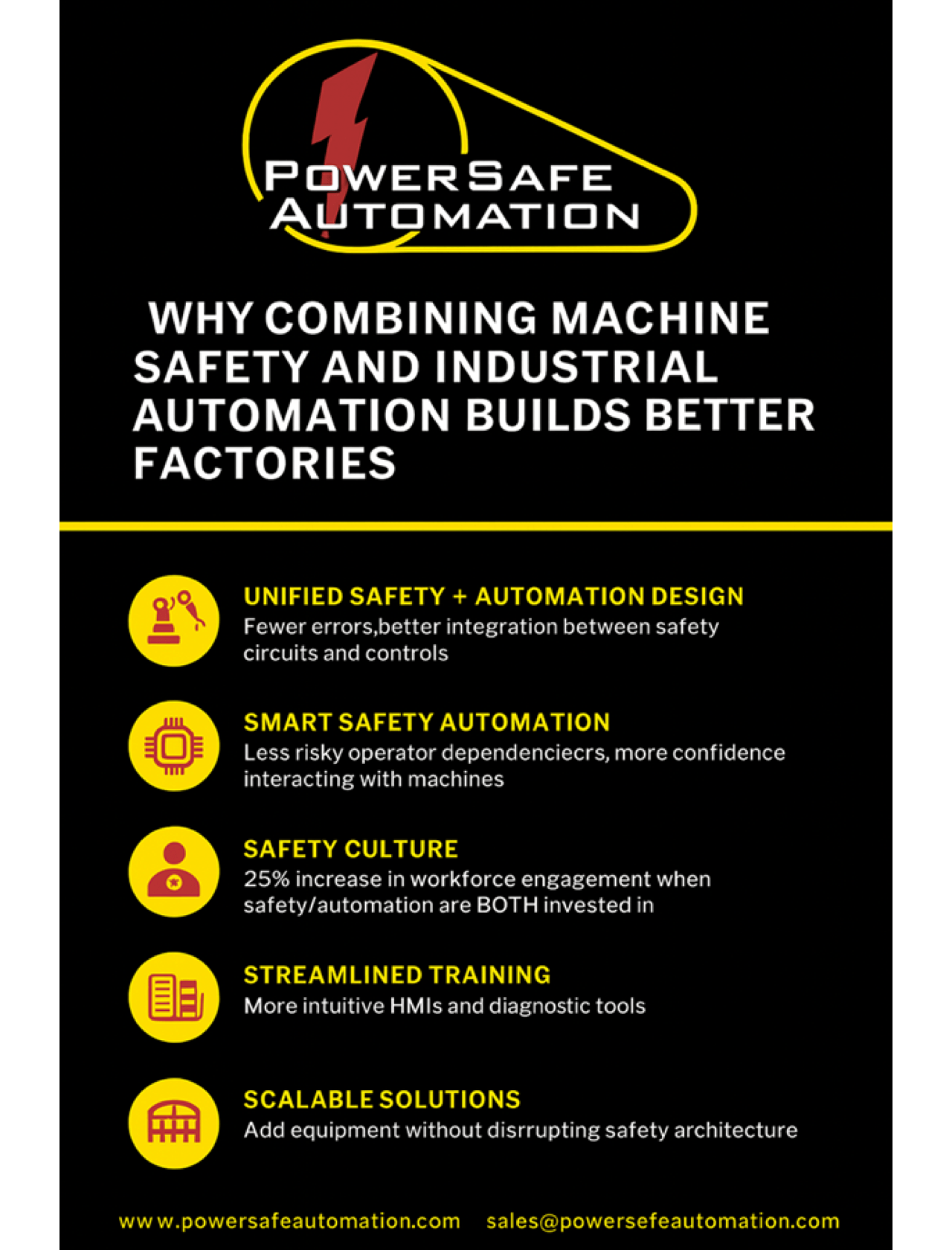