Introduction
Machine guarding isn't just another compliance requirement—it's the cornerstone of a safety-first culture in any manufacturing facility. For Safety Managers, ensuring proper guarding means safeguarding lives, reducing downtime, avoiding costly OSHA citations, and maintaining the trust of your workforce. Yet despite the clear importance, machine-related injuries still account for over 18,000 amputations and serious injuries annually in the United States.
This comprehensive guide walks Safety Managers through the practical, regulatory, and strategic aspects of machine safety guarding. From understanding OSHA standards to leveraging custom turnkey solutions, you’ll learn how to identify gaps in your current setup and implement effective solutions.
Why OSHA Machine Guarding Compliance Matters
The Occupational Safety and Health Administration (OSHA) enforces machine guarding standards under 29 CFR 1910 Subpart O, designed to protect workers from risks like:
-
Rotating parts
-
In-running nip points
-
Flying debris
-
Point-of-operation hazards
OSHA violations related to machine guarding (1910.212) and lockout/tagout (1910.147) consistently rank among the Top 10 most cited violations. Failing to comply not only invites regulatory penalties but also increases the risk of injury, lost productivity, and long-term financial costs.
Types of Machine Guarding
Understanding the available types of machine guarding is the first step in choosing the right system for each application:
1. Fixed Guards
-
Permanently attached barriers
-
Ideal for machines that don’t need frequent access
-
Offer high durability and minimal maintenance
2. Interlocked Guards
-
Automatically shut down machinery when opened
-
Excellent for maintenance zones
-
Encourage safe behavior
3. Adjustable Guards
-
Allow operator adjustments for different tasks or materials
-
Useful in flexible manufacturing environments
4. Self-Adjusting Guards
-
Automatically accommodate varying material sizes
-
Best for changing production volumes
5. Presence-Sensing Devices
-
Use sensors (e.g., light curtains, laser scanners) to detect operator proximity
-
Stops machinery when a person enters a danger zone
6. Two-Hand Controls
-
Requires both hands to activate the machine
-
Keeps hands away from hazardous areas
The 360-Degree Guarding Approach
Most workplace accidents happen because guarding is incomplete—only covering one side or ignoring under-machine access points. A 360-degree guarding strategy eliminates blind spots by protecting all entry points, including overhead and beneath.
Benefits:
-
Full Coverage: Blocks all accidental access points
-
Compliance: Exceeds OSHA, ANSI, and ISO standards
-
Productivity: Safer environments lead to more confident and focused workers
-
Fewer Downtime Events: Better protection during maintenance or servicing
5 Common Machine Guarding Mistakes
1. Using One-Size-Fits-All Guards
Generic guards may not align with your machines, leading to dangerous gaps or workarounds.
Fix: Custom guarding designed to your machine's dimensions, process flow, and operational needs.
2. Compliance Over Functionality
Some setups are compliant but hinder operations, tempting employees to bypass them.
Fix: Incorporate user-friendly features like quick-access doors and visibility panels.
3. Neglecting Non-Production Equipment
Toolroom or maintenance machines often get overlooked—but still pose risk.
Fix: Audit all machinery, not just production lines.
4. Relying Solely on Physical Guards
Physical barriers alone may fail without electrical interlocks and procedural safety.
Fix: Use a layered approach combining physical, electronic, and administrative safeguards.
5. Failing to Update Guards After Changes
Machine upgrades or modifications can invalidate your current guards.
Fix: Conduct post-change risk assessments to ensure updated compliance.
Steps to Implement a Safety Guarding Program
Step 1: Conduct a Risk Assessment
Use tools like JHA (Job Hazard Analysis) or FMEA (Failure Mode and Effects Analysis) to evaluate hazards.
Step 2: Understand the Regulations
Key standards include:
-
OSHA 29 CFR 1910.212 – General Machine Guarding
-
OSHA 29 CFR 1910.147 – Lockout/Tagout
-
ANSI B11 Series – Machine-specific safety
-
ISO 13849 / IEC 62061 – Functional safety
Step 3: Partner with a Guarding Specialist
Work with vendors who offer turnkey solutions—from risk assessments to CAD modeling, fabrication, and installation.
Step 4: Train Your Team
Operators and maintenance personnel should be trained on:
-
Using guards correctly
-
Identifying tampered or faulty guards
-
Lockout/tagout procedures
Step 5: Maintain and Document Everything
Keep records of:
-
Risk assessments
-
Installations and modifications
-
Training sessions
-
Maintenance and inspection logs
Technology-Driven Guarding Solutions
Modern machine guarding integrates seamlessly with smart factory systems:
-
Laser Scanners: Create flexible virtual zones
-
Light Curtains: Detect any interruption and stop machinery
-
Smart Sensors: Alert teams to tampering or malfunction
-
Safety PLCs: Centralize safety logic across machines
These technologies allow for increased safety without compromising functionality, especially in high-speed, automated environments.
How Custom Guarding Solves Legacy Challenges
Older machines often can’t accommodate off-the-shelf guards. Instead of replacing reliable equipment, custom-designed guards offer a cost-effective way to:
-
Preserve legacy investments
-
Ensure OSHA compliance
-
Improve operator safety
-
Integrate safety devices (e.g., sensors, interlocks)
PowerSafe Automation, for example, conducts on-site assessments, creates 3D CAD models, and delivers a full scope-of-work document detailing optimal guarding solutions.
Case Study: Real-World Impact of Smart Guarding
A Tier-1 automotive supplier reported:
-
63% reduction in hand injuries
-
Zero OSHA citations during inspection
-
Faster maintenance with modular, interlocked guards
Their system included:
-
Fixed mesh panels
-
Safety PLCs
-
Interlocked access doors
-
Light curtains and laser scanners
This shows how integrated, comprehensive guarding strategies not only protect workers—but streamline production.
Creating a Culture of Safety
As a Safety Manager, your role goes beyond technical compliance. You’re shaping a workplace culture that prioritizes:
-
Awareness: Workers who recognize unsafe conditions
-
Accountability: Teams that report and fix issues
-
Engagement: Employees trained, informed, and invested in safety
Final Thoughts
Machine guarding isn’t just about barriers—it’s about people. Every fixed guard, light curtain, or interlock switch is a step toward a safer, more productive facility. Investing in OSHA-compliant and custom-fitted guarding not only fulfills regulations but builds a foundation of trust, responsibility, and operational excellence.
Take the Next Step: Free Risk Assessment
Is your facility’s guarding system truly keeping your team safe?
Contact PowerSafe Automation today for a guarding assessment and discover custom-engineered solutions built for your unique equipment.
Let’s build a safer manufacturing environment—together.
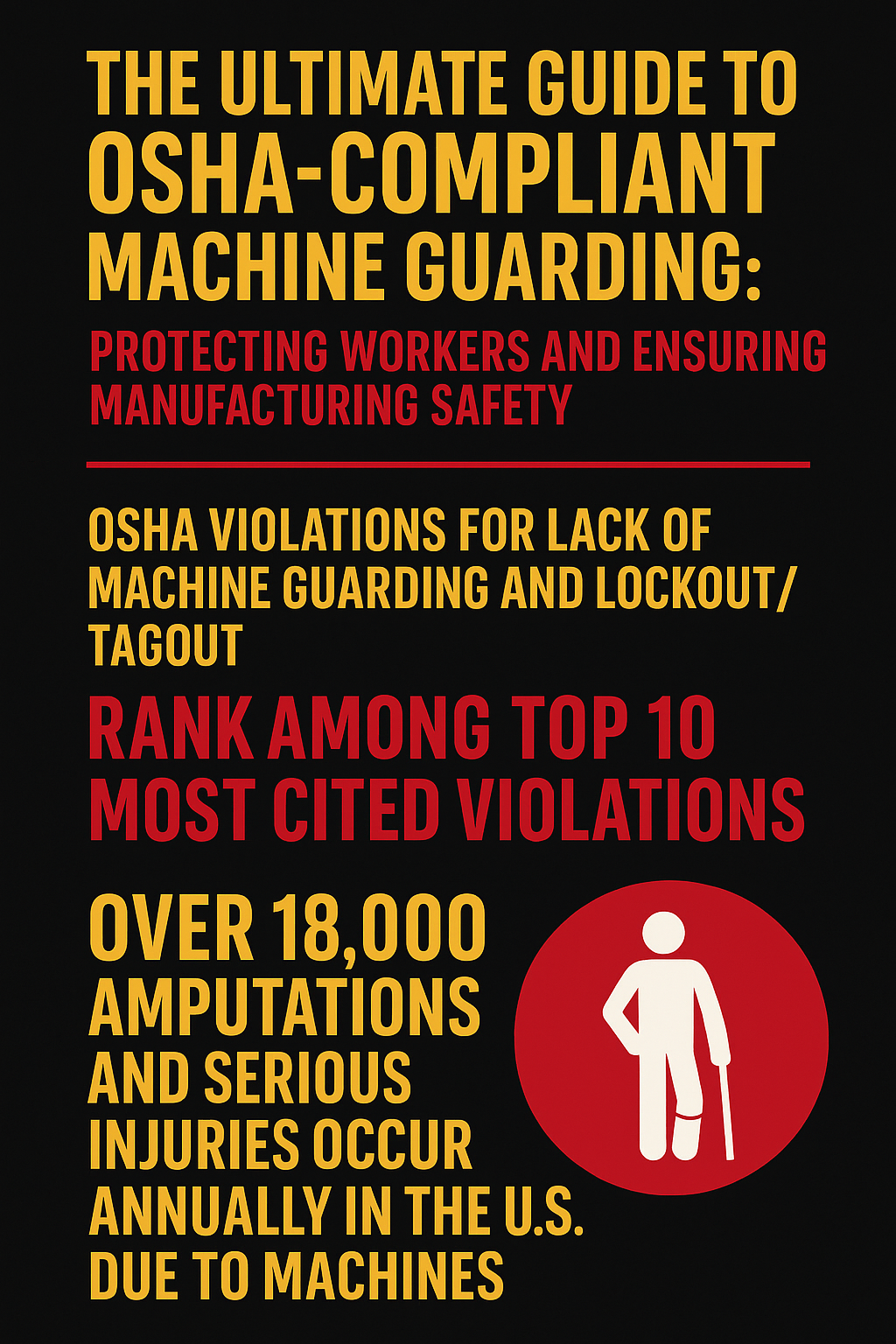