Introduction
Forming and sizing mills are critical components in metal processing and tube manufacturing operations. However, their high-speed, high-force operations also make them one of the more hazardous areas on the shop floor. For Safety Managers, ensuring robust machine safety measures in these mills isn’t just a regulatory requirement, it's a vital step toward minimizing risk, preventing injuries, and maintaining operational uptime.
In this post, we’ll break down the key machine safety guarding requirements for forming and sizing mills and provide actionable guidance to help you enhance safety and compliance in your facility.
Why Forming and Sizing Mills Require Specialized Safety Guarding
Forming and sizing mills use a series of rolls to shape and size metal products such as tubes and pipes. The nature of this equipment means:
- Rotating components (rollers, shafts) pose entanglement risks.
- Pinch points can lead to crushing or amputation injuries.
- Flying debris from material breakage or roll failure can injure nearby workers.
- Manual adjustments or maintenance often expose workers to moving parts.
Because of these risks, OSHA, ANSI, and other standards organizations require specific safeguards to protect operators and maintenance personnel.
Applicable Safety Standards
To ensure compliance and best practices, Safety Managers should be familiar with the following standards:
- OSHA 1910 Subpart O – Machinery and Machine Guarding Mandates general requirements for machine guarding across all industries.
- ANSI B11.0 – Safety of Machinery A foundational safety standard providing risk assessment principles and hazard control measures.
- ANSI B11.8 – Safety Requirements for Manual Milling, Drilling, and Boring Machines While not specific to tube mills, many principles apply to rotating machinery with similar hazard profiles.
- ISO 13857 – Safety Distances Defines minimum safety distances to prevent access to hazardous machine zones.
Key Machine Guarding Requirements for Forming and Sizing Mills
Here are the top areas where guarding should be implemented:
Roll Stands and Pinch Points
Guarding must prevent access to rotating rolls, gears, and shafts. Consider fixed barriers made of steel or polycarbonate, interlocked movable guards where access is occasionally needed, or light curtains or area scanners for high-frequency access zones.
Entry and Exit Points
Where material enters or exits the mill, install tunnel guards or angled barriers to deflect material and prevent hand entry. Emergency stops within reach but outside hazard zones should also be installed.
Maintenance Access
Ensure guards are easy to remove with tools (per OSHA 1910.219). All guards need to be interlocked so power is cut before access is possible. Follow all Lockout/Tagout (LOTO) procedures.
Flying Debris Protection
High-speed rolling can occasionally lead to material failures. Use polycarbonate or wire mesh guards rated for impact. Also consider overhead barriers where feasible to protect from upward ejection.
Conducting a Risk Assessment
Before installing or upgrading machine guarding, perform a formal risk assessment that includes:
- Identifying all potential hazards during normal operation, setup, and maintenance.
- Evaluating severity and likelihood of each risk.
- Applying the hierarchy of controls—starting with elimination, followed by engineering controls (guards), then administrative controls and PPE.
A well-documented risk assessment not only supports compliance but also helps justify safety investments to leadership.
Best Practices for Safety Managers
- Audit Your Existing Guarding: Use a checklist based on ANSI B11 standards to assess current machine guarding effectiveness.
- Engage Operators and Maintenance Teams: Their input is vital for identifying overlooked hazards and ensuring new guards don’t hinder productivity.
- Invest in Modular Guarding Systems: These offer flexibility for evolving equipment layouts while maintaining compliance.
- Train Continuously: Ensure all affected employees understand the purpose and proper use of machine guards.
Conclusion
Forming and sizing mills are essential yet potentially dangerous equipment in manufacturing facilities. As a Safety Manager, ensuring they are properly guarded is critical to preventing injuries, reducing downtime, and maintaining regulatory compliance. By understanding applicable standards and implementing best practices in machine guarding, you can significantly improve your facility’s safety culture and operational resilience.
To listen to the video on this Machine Safety for Mills blog
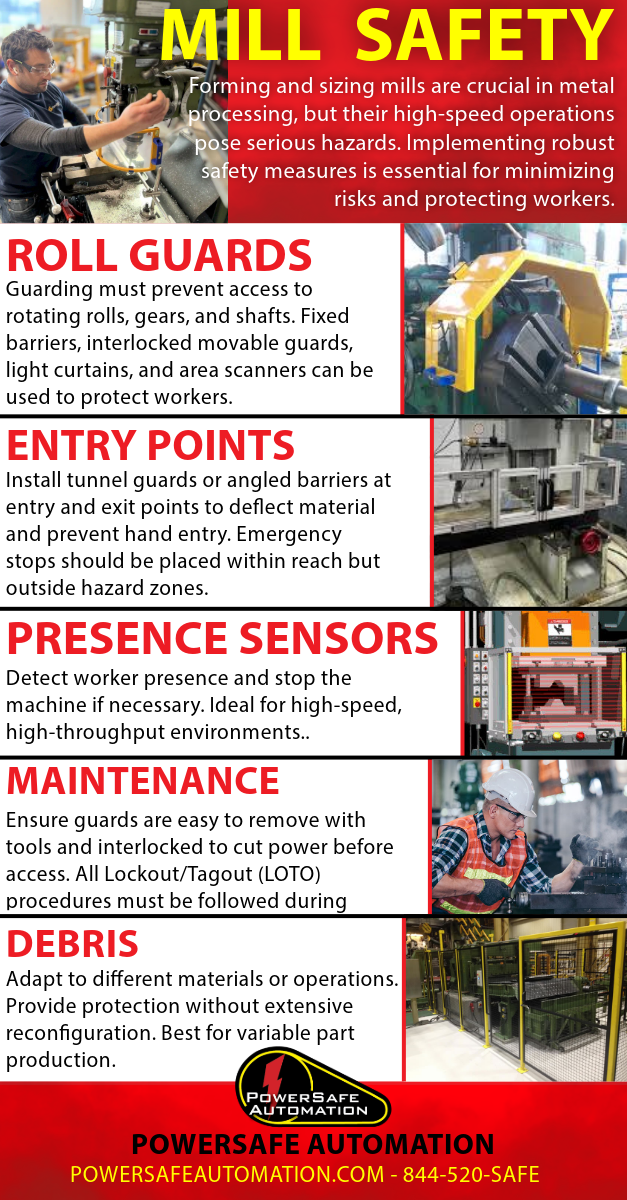