Why Ergonomic Safety Is Critical in Modern Manufacturing
In today’s industrial landscape, safety managers face increasing pressure to balance productivity, compliance, and worker well-being. Amid fast-moving machinery and demanding workflows, one aspect often overlooked is ergonomic safety—a strategic tool that not only prevents injuries but also supports operational efficiency and boosts morale.
Ergonomic safety is about designing jobs, tools, and workspaces that align with the natural movements and limitations of the human body. In manufacturing, poor ergonomics can lead to musculoskeletal disorders (MSDs), high turnover, and even increased risk of machine-related accidents.
In this guide, we’ll explore the essentials of ergonomic safety, highlight its synergy with pedestrian safety and machine guarding, and offer actionable tips for implementation in your facility.
Understanding Ergonomic Safety: The Worker-Centric Approach
At its core, ergonomic safety minimizes physical strain by adapting the environment to the worker—not the other way around. This means evaluating how repetitive motion, awkward postures, overexertion, and static loads affect employee health over time.
Common Ergonomic Hazards in Manufacturing:
-
Repetitive reaching around guarding
-
Poorly placed controls causing awkward positions
-
Manual lifting in cramped or obstructed spaces
-
Standing for prolonged periods on hard surfaces
These issues are not only physically damaging but can reduce focus, increase errors, and raise the likelihood of incidents near dangerous machinery.
Engineering Ergonomic Solutions: Practical Upgrades
1. Adjustable Workstations
Workstations should accommodate a range of body types and movements. Starting with a height range of 29” to 39”, an ideal adjustable station includes electric lifts that add ±6” of flexibility, reducing the need for awkward bending or reaching.
Additional workstation upgrades include:
-
Anti-fatigue mats to reduce pressure on joints
-
Task lighting to ease visual strain
-
Organizational tools for tool accessibility and efficiency
2. Ergonomic Carts and Flow Racks
Carts should be designed to reduce pushing and pulling forces. Adding swivel casters, adjustable handles, and optimal shelf heights can prevent overexertion injuries.
Flow racks can also streamline material handling by using gravity-fed systems that minimize lifting and reaching.
3. Auto-Lift Tables
One of the most impactful innovations in ergonomic manufacturing is the auto-lift table. These devices eliminate manual lifting by adjusting to the worker’s needs through electric or hydraulic systems.
Benefits include:
-
Adjustable height settings for diverse tasks
-
Increased lifting speed and load capacity
-
Fail-safe safety mechanisms and emergency stops
-
Reduced back injuries and fatigue
Companies implementing auto-lift tables have reported measurable improvements in both safety and productivity.
The Ergonomics–Pedestrian Safety Synergy: A Hidden Win for Machine Guarding
Ergonomics and pedestrian safety may seem like separate initiatives—but together, they offer a powerful safety strategy. Poor ergonomics often push workers into unsafe zones, increasing pedestrian-vehicle collisions or machine contact.
Where They Intersect:
Ergonomic Design | Pedestrian Safety Benefit |
---|---|
Well-placed controls | Reduces unsafe movement near operating equipment |
Adjustable guard access | Encourages proper lockout/tagout and minimizes awkward entry |
Optimized work zones | Keeps employees within safe zones, away from high-traffic areas |
Fix: Integrate ergonomic reviews into continuous improvement processes.
2. Ignoring Worker Feedback
Mistake: Relying solely on managers or engineers for ergonomic assessments.
Fix: Involve frontline workers—they know where the pain points really are.
3. Over-Focusing on Office Ergonomics
Mistake: Neglecting industrial environments while focusing on desks and screens.
Fix: Prioritize physical jobs like assembly, machining, and packing lines.
4. Buying Equipment Without Assessment
Mistake: Investing in tools before understanding the specific risk.
Fix: Conduct ergonomic assessments like REBA or RULA before purchasing.
5. Failing to Measure Results
Mistake: Implementing changes without tracking injury data or productivity.
Fix: Track MSD rates, worker feedback, and ROI on ergonomic investments.
Quantifiable Benefits of Ergonomic Integration
Companies that integrate ergonomic safety with broader safety goals see significant returns:
-
Fewer injuries: Reduction in overexertion and struck-by incidents
-
OSHA compliance: Meets standards like 1910.212 (Machine Guarding)
-
Higher productivity: Less downtime and fewer worker absences
-
Improved morale: Employees feel safer and more valued
Practical Steps for Safety Managers: Implementing Ergonomic Safety
-
Conduct a Joint Safety Audit Use ergonomic tools like REBA and map pedestrian/machine zones.
-
Involve Cross-Functional Teams Collaborate with maintenance, engineering, and traffic planners.
-
Redesign for Dual Purposes Choose safety solutions that balance access, visibility, and ergonomics.
-
Train with Real-World Scenarios Use digital simulations and live walkthroughs to reinforce behaviors.
Final Thoughts: Ergonomics Is a Strategic Safety Lever
Ergonomics is not just about comfort—it’s about protecting people, increasing efficiency, and building a resilient safety culture. When combined with pedestrian safety and machine guarding strategies, ergonomic design becomes a competitive advantage in manufacturing.
Want Expert Support?
At Power Safe Automation, we specialize in turnkey machine guarding and ergonomic safety solutions. Contact us for a facility-specific risk assessment and discover how small changes can lead to big results.
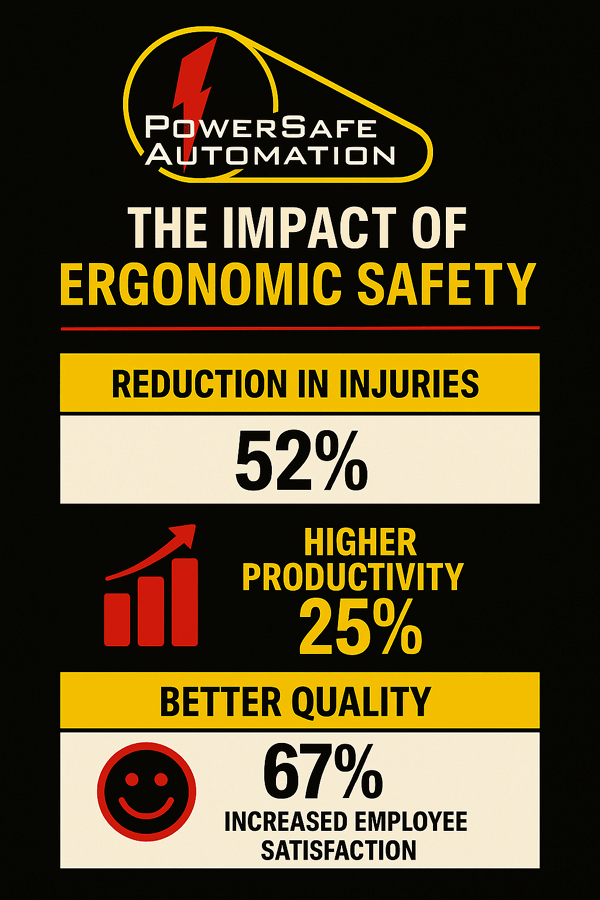