Machine Guards and Shields
User-Friendly for Machinists
The forgotten machines, the low hanging fruit, the experienced machinists domain...whatever the reason is, these machines need to be guarded regardless of skill set, which OSHA does not discriminate against. This turnkey machine shop guards along with anti-start devices for safety switches and LED machine lights or industrial work lights, are all user-friendly from a machinist's perspective.
Ready to Purchase and Get Protected Today
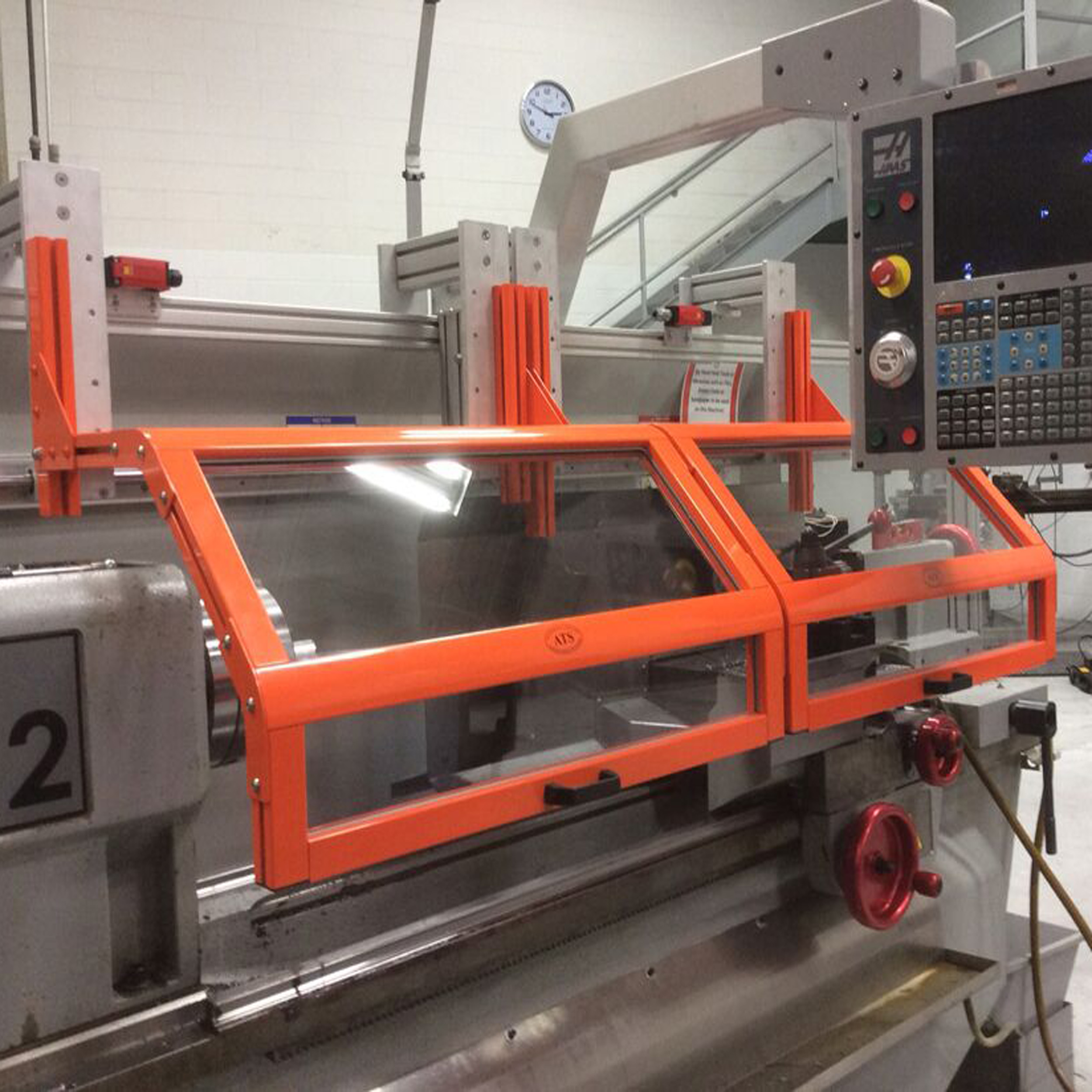
Manual Lathe Guards
Chuck guards and lathe guards are made with safety orange powder coated aluminum with clear polycarbonate panels, designed as a lid-assisted hinge or a linear rail sliding guard to be mounted to the machine or the floor. These units come with safety switches to work with machines up to 480v for primary machining operations and an authorized bypass key for secondary tasks such as polishing, deburring, and filing to prevent cuts from sharp metal curling, pull-in, wrapping, or cut hazards, and oil or coolant spraying at operators. Offering added protection or chip containment, vinyl strips are added when the flexibility is needed at the tool rest. This machine guarding can be used on most brands of lathes such as Harding, Jet, Baileigh, and Kent..
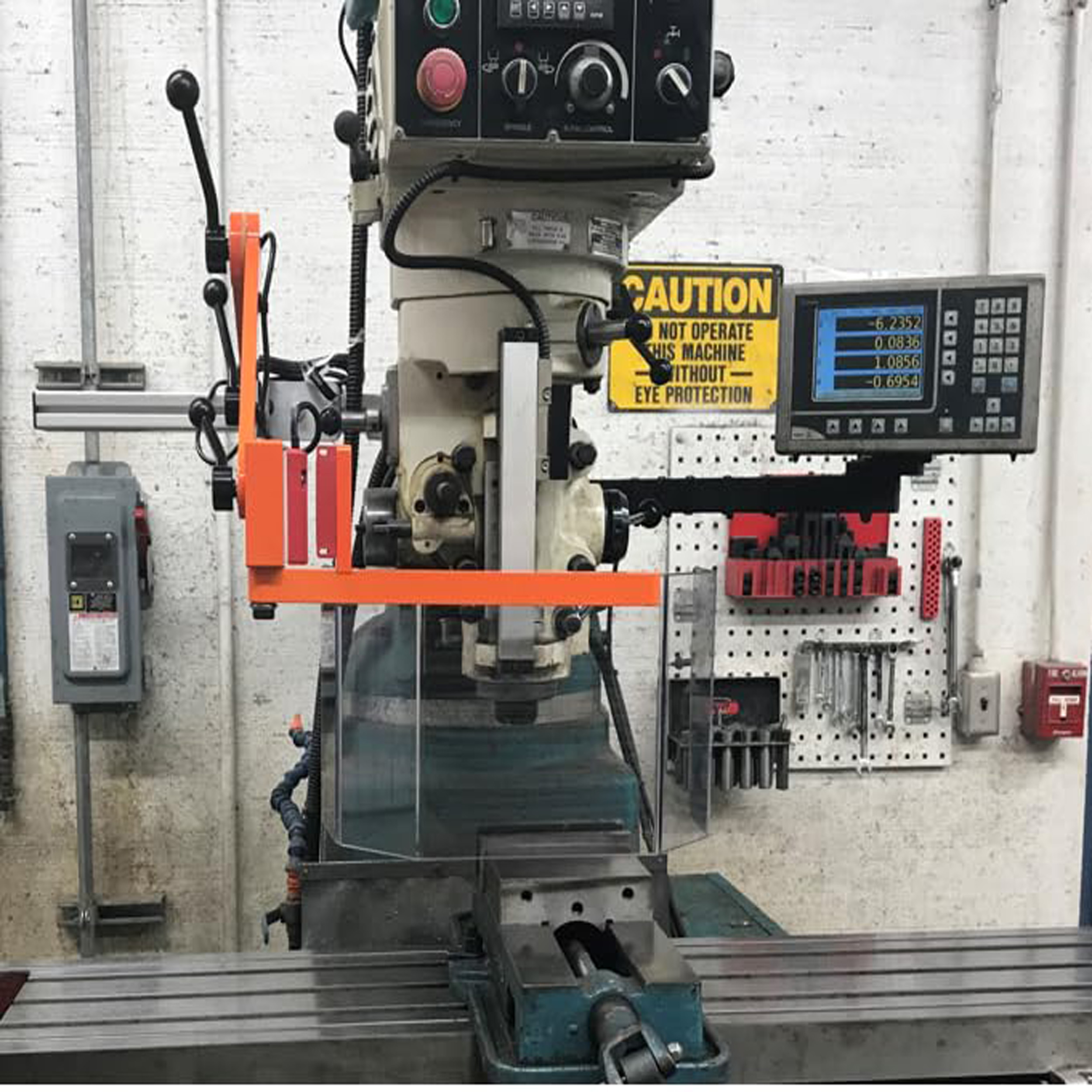
Milling Machine Guards
Modular machine guarding for manual mills and CNC bed mills with options to mount to the ram or head are used to prevent hot flying chips, hazards like entanglement, cut, crush, and shear points, as well as keeping coolant from spraying out. The hi-vis aluminum structure designed with articulating arms help make the guarding user-friendly for even the most experienced machinists, giving them flexibility for countless tooling, fixturing, and material size options. These units are equipped with safety switches rated from 110vac when using power feed units up to 480v interrupt the spindle motor to prevent hazards at the spindle. Brands such as Bridgeport, Jet, Lagun, Clausing, Trak, and Sharp mills are just some of the types that can be adapted to a safer operation.
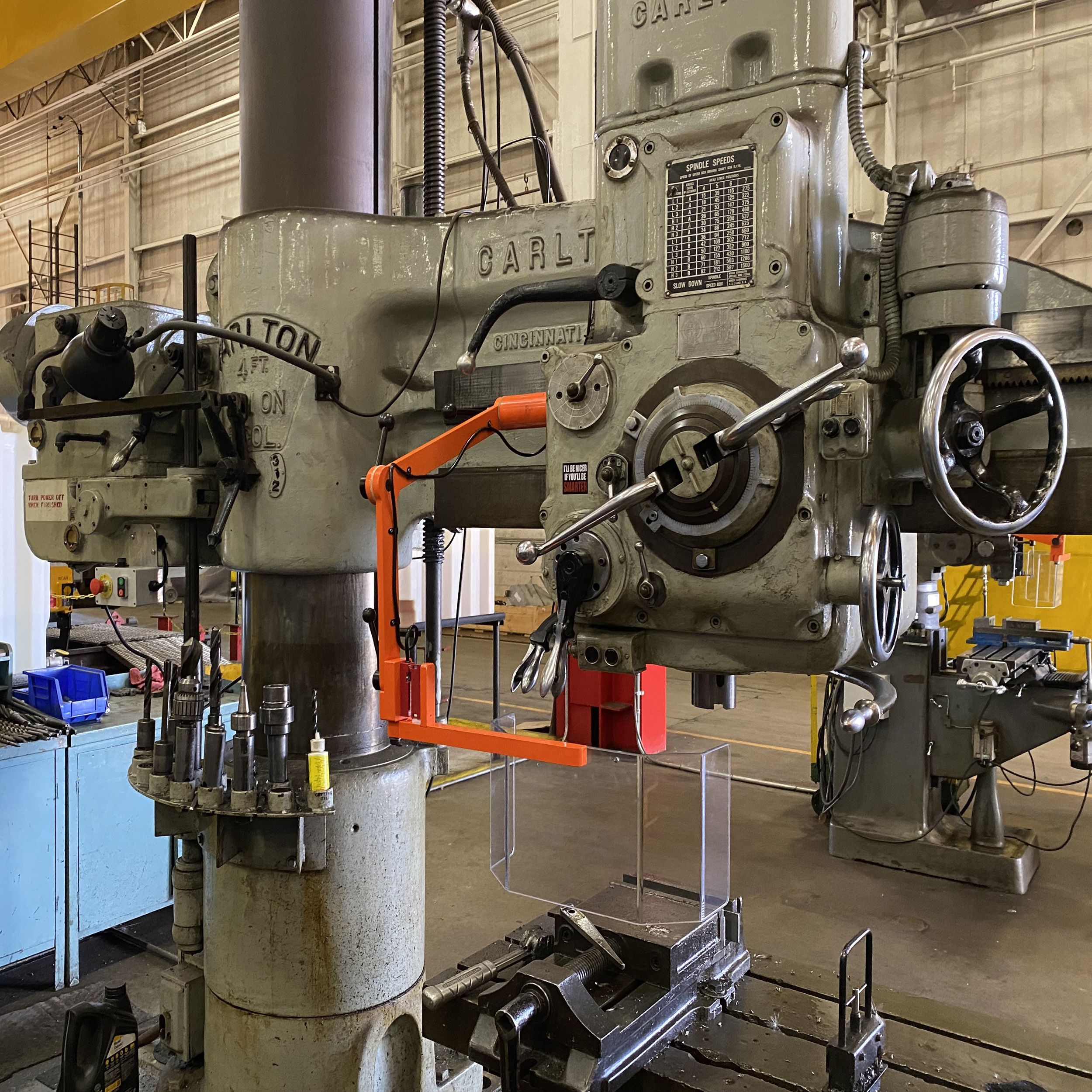
Radial Arm Drills and Drill Press Guards
Adjustable column mounted and universal pattern mounted guards minimize metal shavings from the operator, reducing the opportunity for cut points at the drill bits, entanglement hazards at the rotating spindle or chuck, or trip and fall hazards from spraying of coolants. Safety switches are supplied to increase the level of safety when using machines like Jet, Delta, Powermatic, Clausing, and Baleigh brand drill presses. For added protection on large radial arm drills, safety mats or physical guarding can be added to the back of the machine.
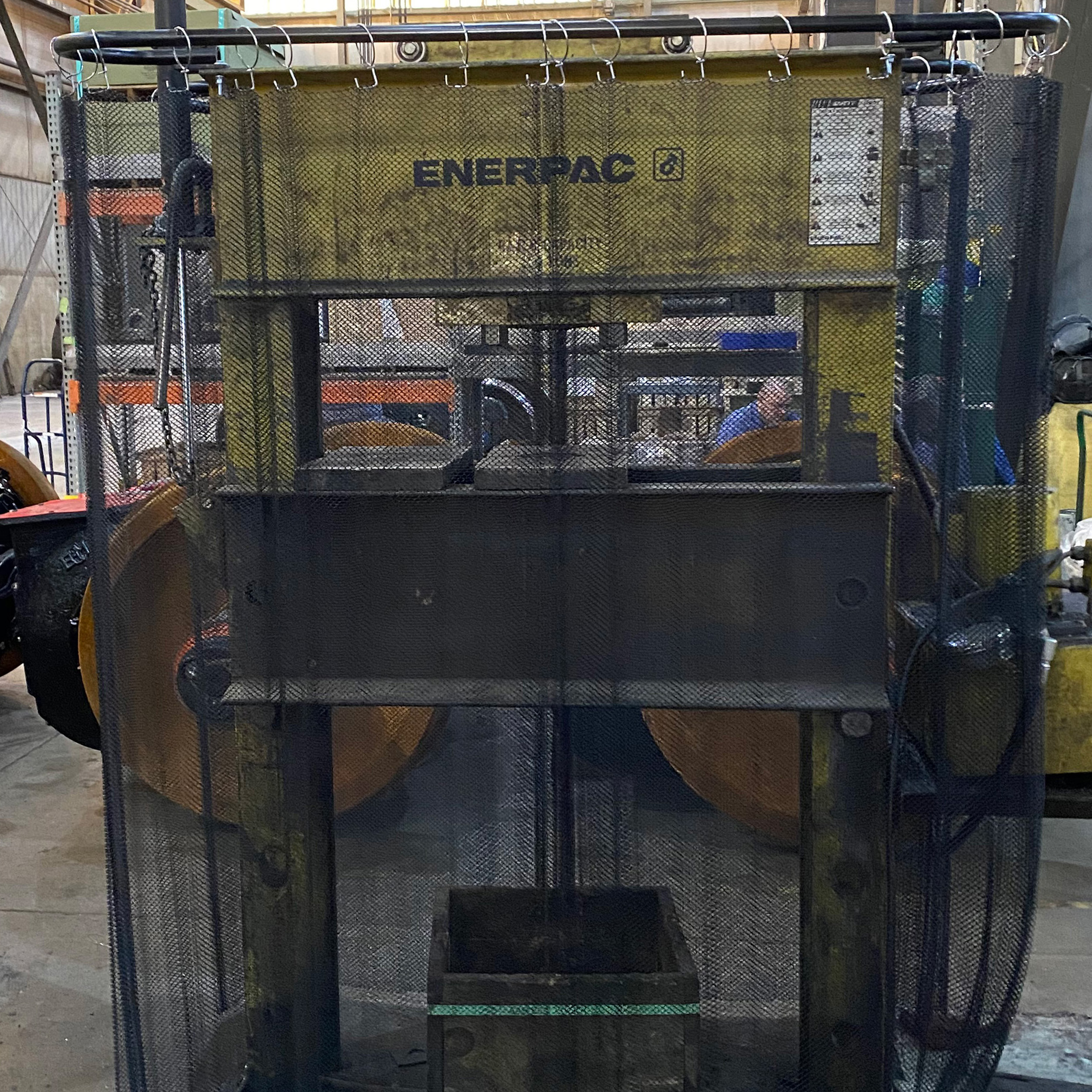
General Shop Press Safety Curtains
Steel mesh ejection or ballistic curtains for hydraulic shop presses are used to guard against material ejection like parts under pressure or fragments from breakage while pressing. These curtains provide flexibility for long parts, which still provide visibility of the operation. Designed with a split curtain and rod front and back for optimized protection from the ram or die when pressing protruding parts. This option does not offer a safety switch. Designs can be offered with point of operation guarding with a safety interlocked door using clear polycarbonate panels for low profile parts when verification of safeties are required.
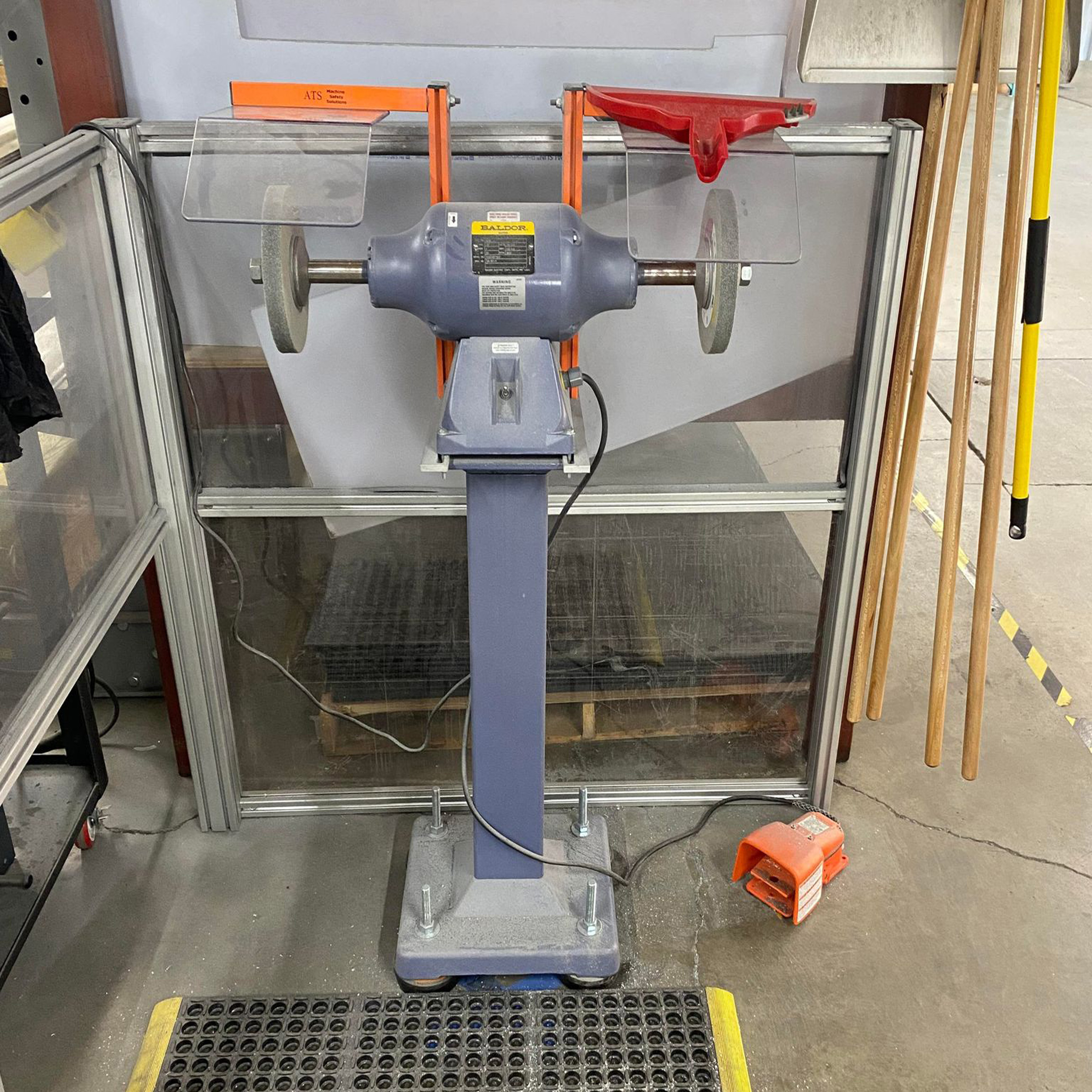
Bench Grinder and Buffer Shields
Machine shields are used to protect eyes, face, and body by preventing flying debris or fragments, sparks, or rotating grinding wheels from contacting operators. The deflectors angle the material ejection downward and help manage widespread mess as well. Metal framed polycarbonate shields allow for visibility of work and side guards can be added for additional protection. Tongue guards should be adjusted within ¼” and work rests within 1/8”.
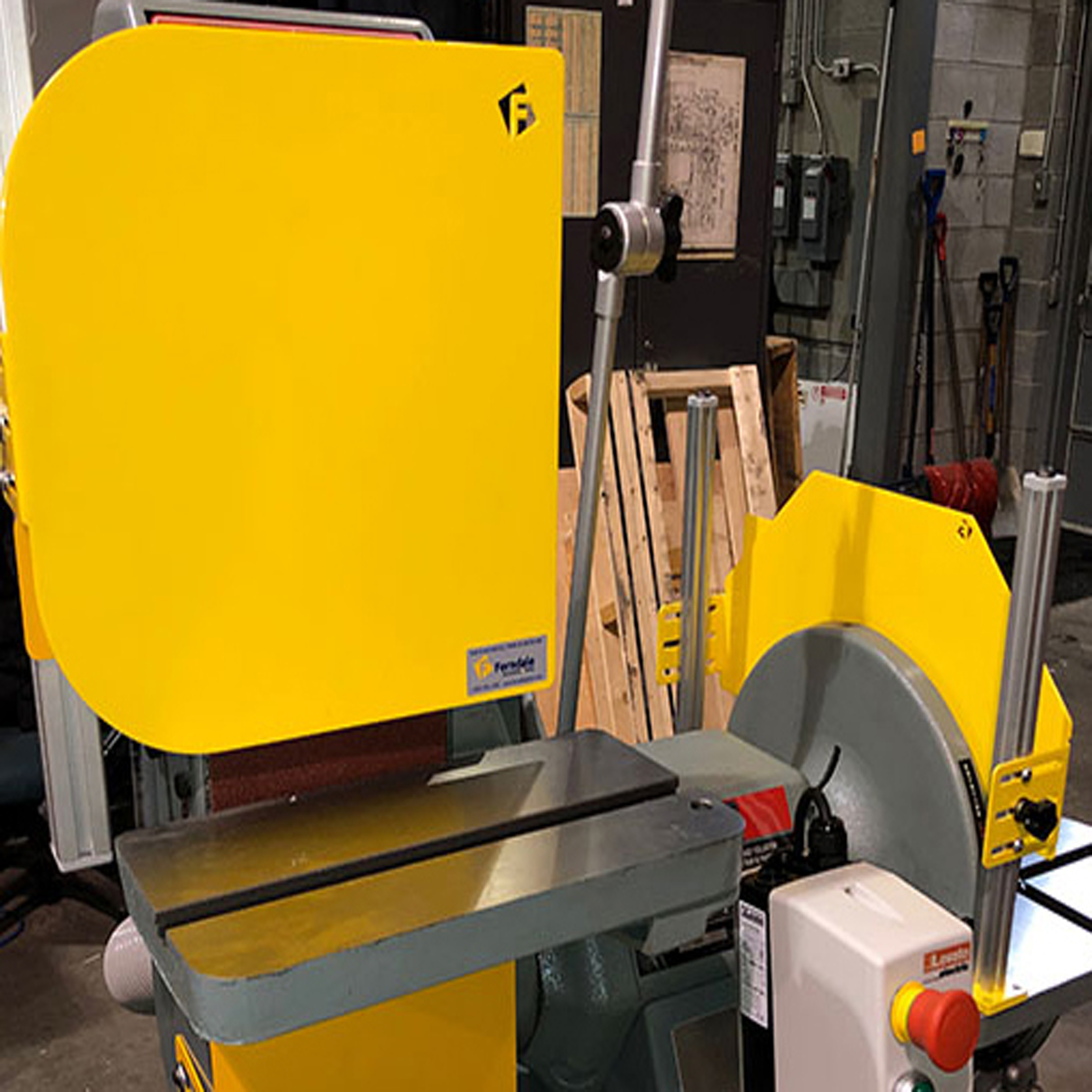
Belt and/or Disc Sander Shields
Adjustable guards designed for single use or combination machines for a variety of sanding belt widths and disc diameters require protection covering the unused areas of the sanding surface when performing secondary finishing operations. This is done to prevent fingers and hands from cuts, burns, abrasions when using this type of equipment, as well as nip point and amputation from entanglement of clothes where the belts or discs meet the pulley.
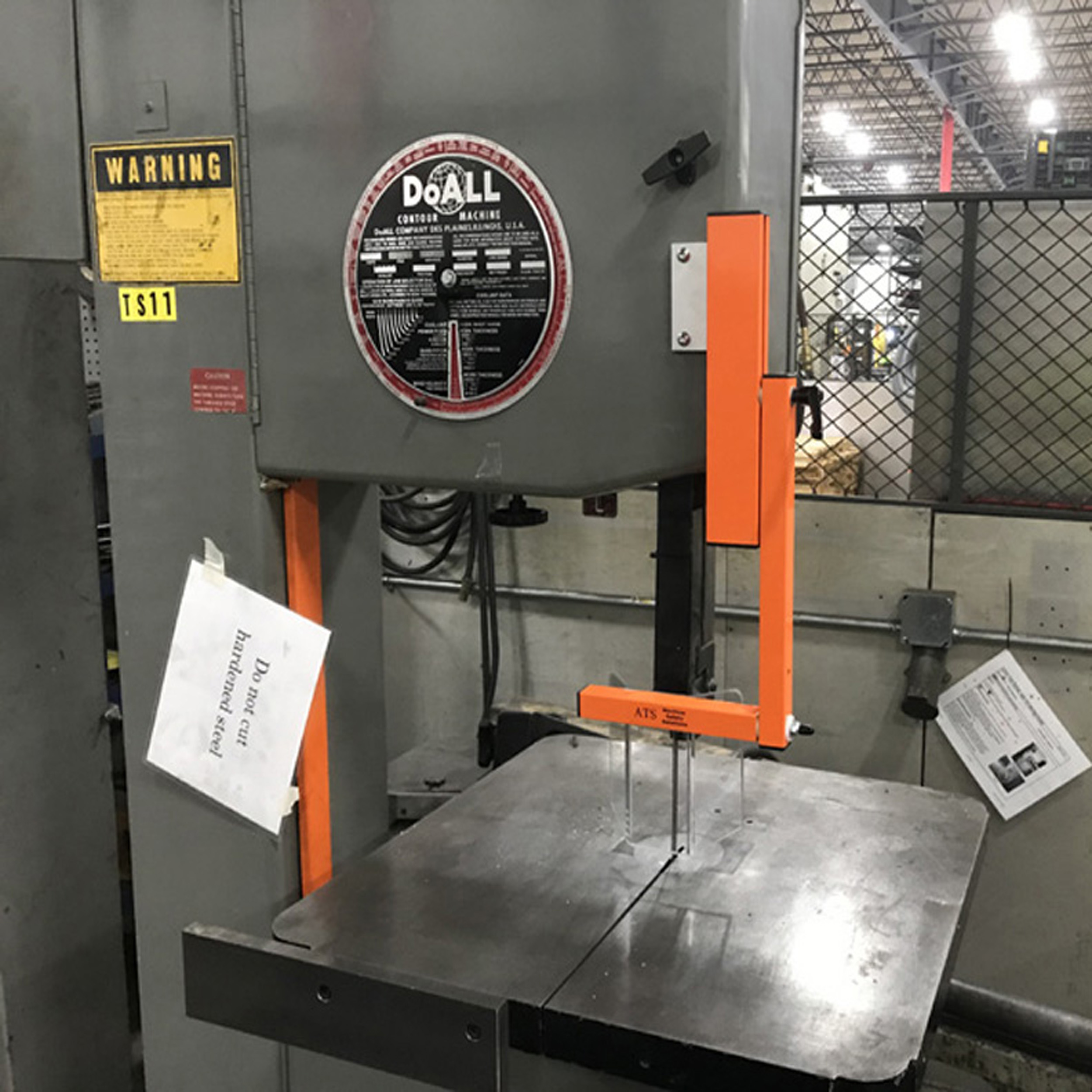
Vertical Bandsaw Shields
For shop use bandsaws, shields or blade guards with polycarbonate panels for clear view to the part providing multi-directional adjustability with polycarbonate panels are used to prevent accidental contact with the moving saw blade during material feeding. This contact can result in hazards such as cuts or lacerations or even amputation and keep metal shavings down during cutting cycles. Hi-vis orange extrusion without a safety switch is used due to the variety of product shapes.
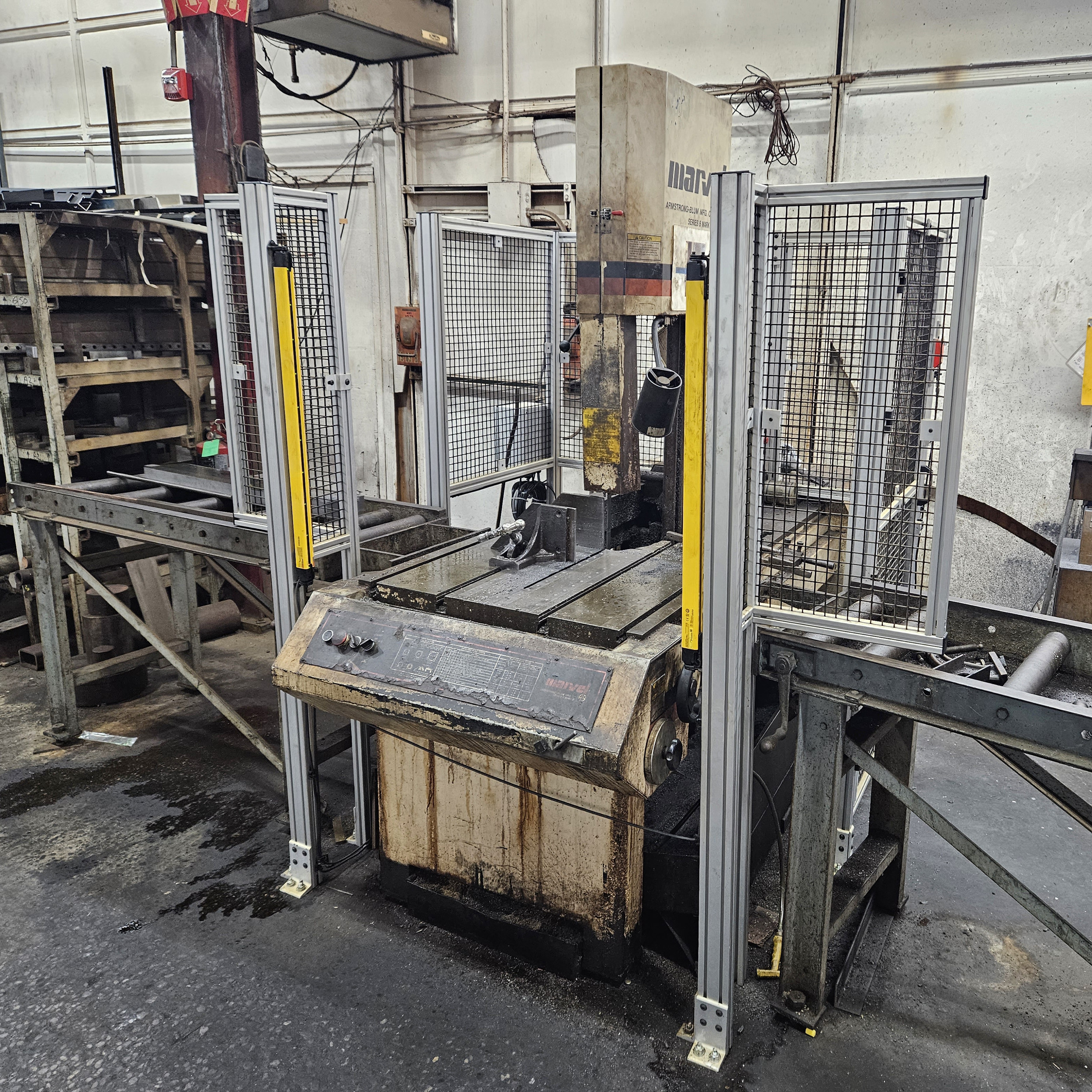
Vertical Bandsaw Guards
Large production use vertical bandsaw integrated with safety light curtains mounted to rigid posts at point of operation and machine guarding around sides and back preventing cutting, shearing, or entanglement hazards while still giving access to the chip tray and blade changes without interrupting the hydraulics functionality. Cycle start and emergency stop buttons can be added remotely if controls are located inside the safety zone.
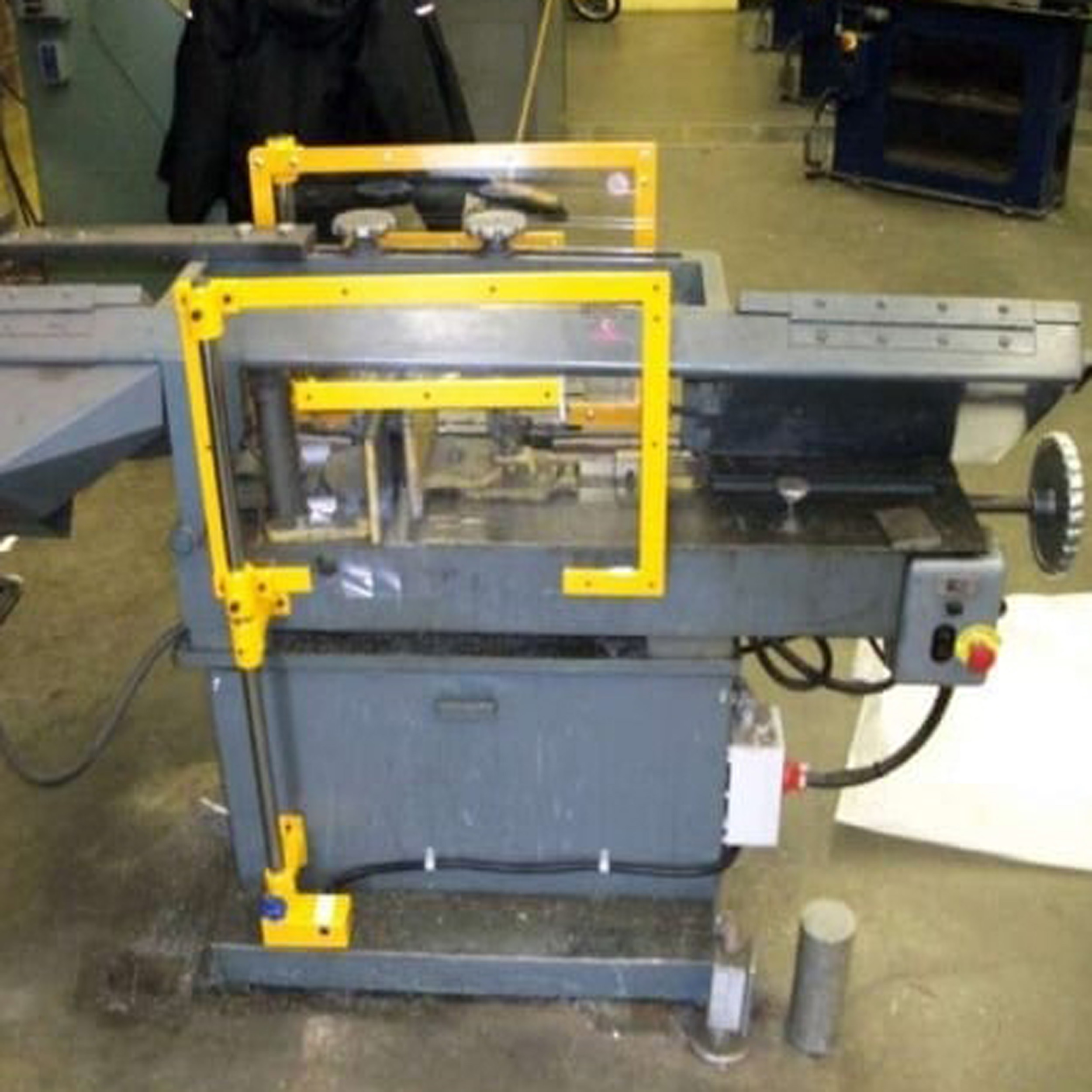
Horizontal Bandsaw Shields
Shop size equipment, safety switched hinged machine guards with polycarbonate panels for clear view to part with vinyl strips for material variability is used to prevent from accidental contact with the saw blade. Exposure to shear and cut points, as well as loss of limb is minimized with these hi-vis safety yellow safety guards.
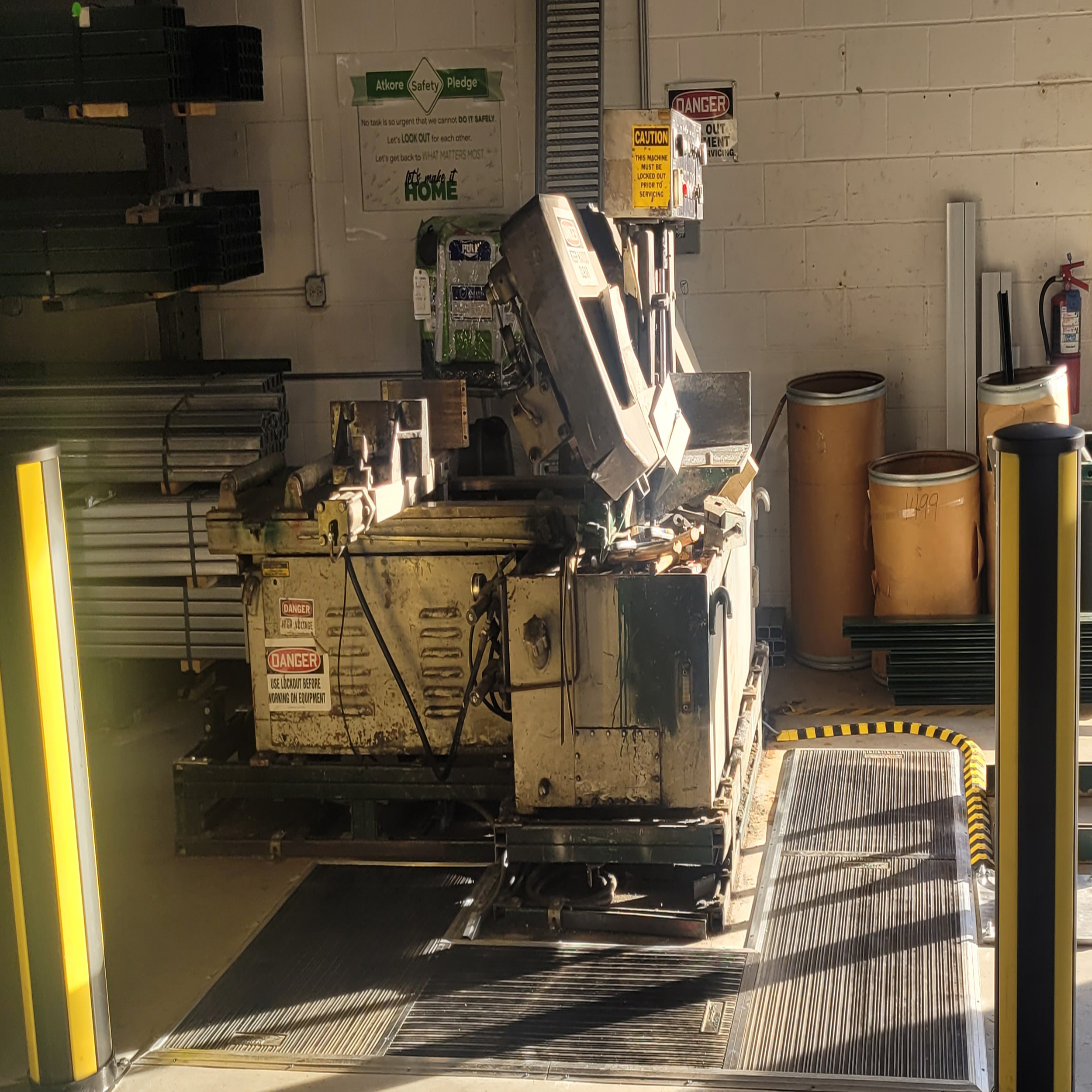
Horizontal Bandsaw Guarding Systems
Large production use equipment, safety switch mats or safety laser scanners coupled with protective bollards on the front, physical safety guarding on the back, and a remote blade start operator station with an e-stop on a pedestal is developed to keep operators from the hazardous cutting and clamping areas due to reach-in or loose clothing. The system uses the blade start/stop function allowing for hydraulic energy live for blade change operations.
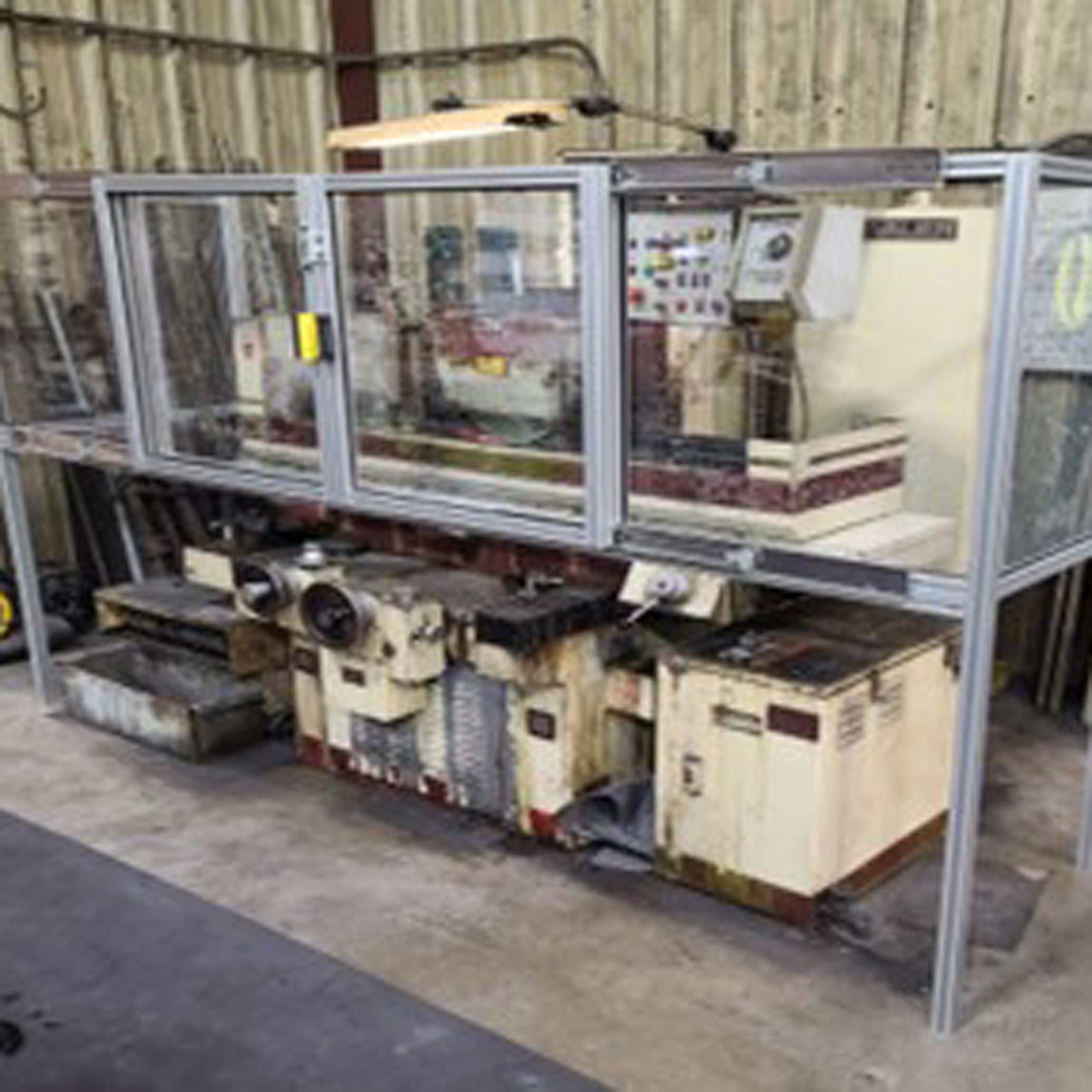
Surface Grinder Guards
Machine safety enclosures are used to prevent nip points, cuts, and burns found when working in direct contact with the grinding wheel. This guarding is also used to mitigate against shattering or exploding wheels due to defects in the wheel, coolant puddling, or too much force on the part, and thrown objects when the magnetic chuck is not activated. These guards typically are not equipped with safety switches due to the grinding wheel safety concerns around temperature requirements.
Check out ANSI B7.1 or under ANSI B11.9 for more information
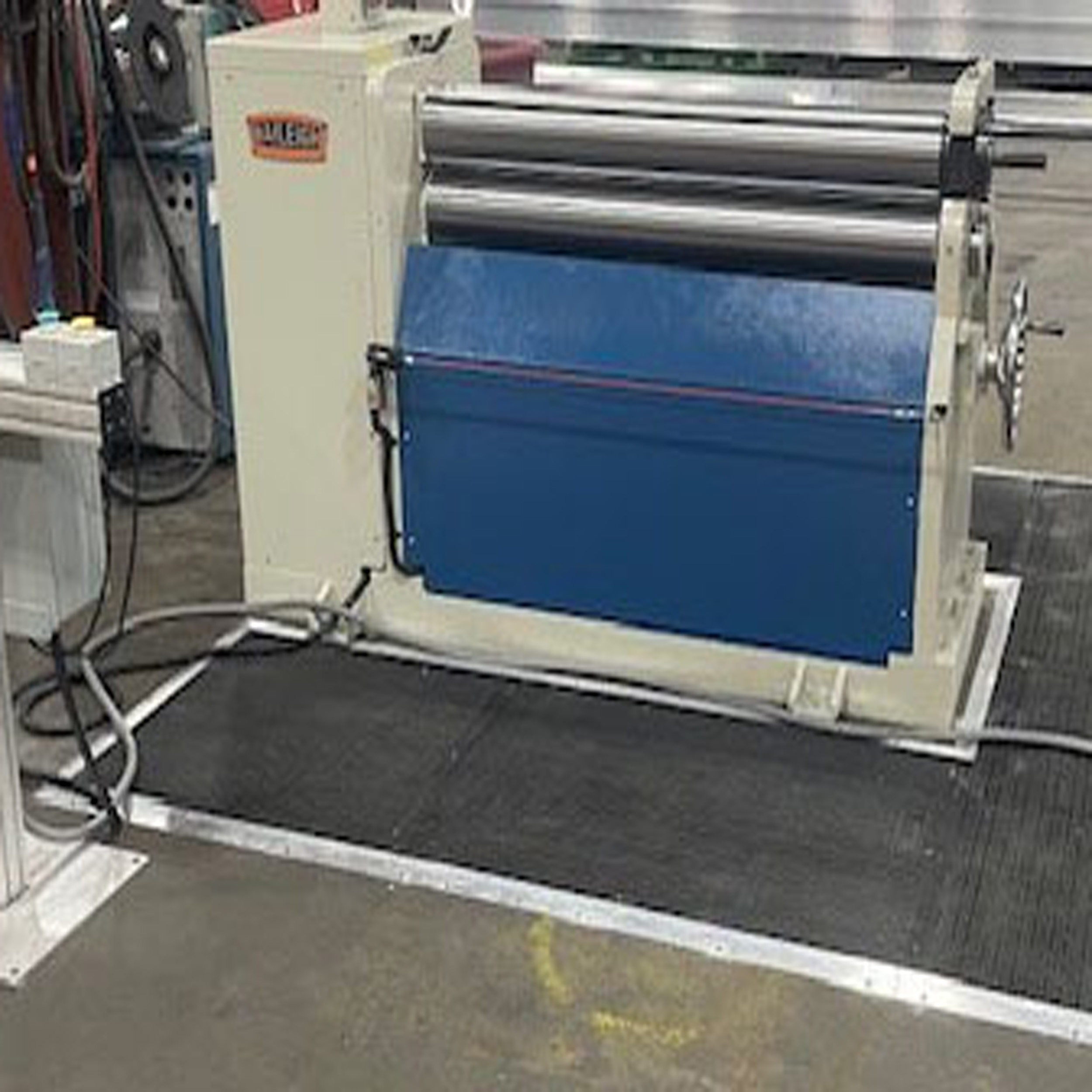
Plate Roller Safety
Machine safety packages to protect operators and the third person from in-running nips producing crushing hazards, pinch points, or entanglement on power-driven rolling forming or bending equipment. These solutions include custom designed safety mats surrounding the rollers monitored by a safety controller and a pedestal-style 2-hand operator control stand to activate rollers. Emergency rope pull stops can be included for added protection.
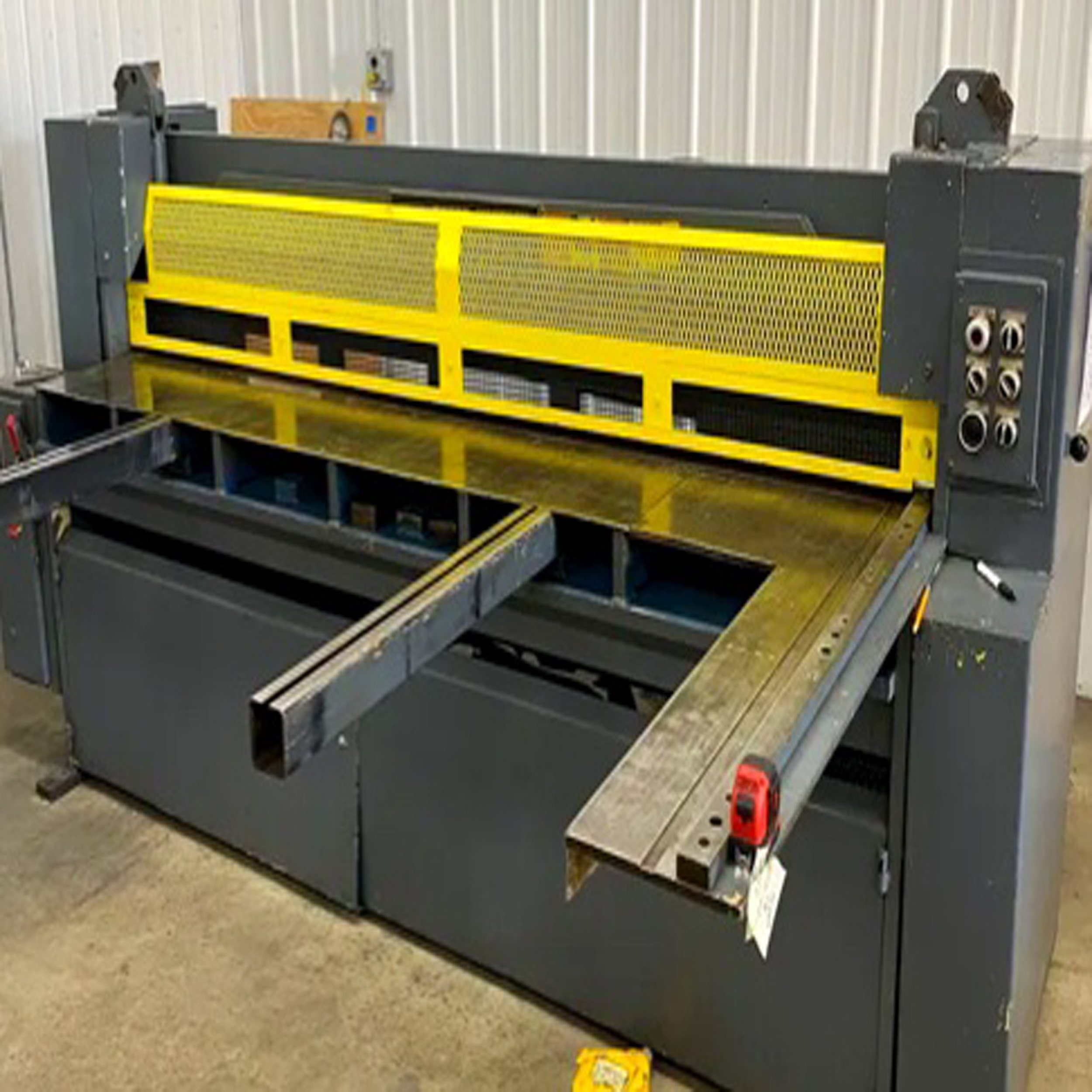
Shear-Nip Guarding
Hi-strength, round bar style finger guards or nip guard custom fit to bolt on at point of operation protecting workers from cut or laceration, shear, and crush hazards, as well as amputations at the moving blade when operating a shear. Guards should also be added to the sides where gears, sprockets, and chains are exposed, and perimeter guarding with safety gates and safety switches tied into the emergency stop circuit to be custom fabricated prevent access from the back of the machine.